7 Tips To Reduce Warehousing Operations Costs
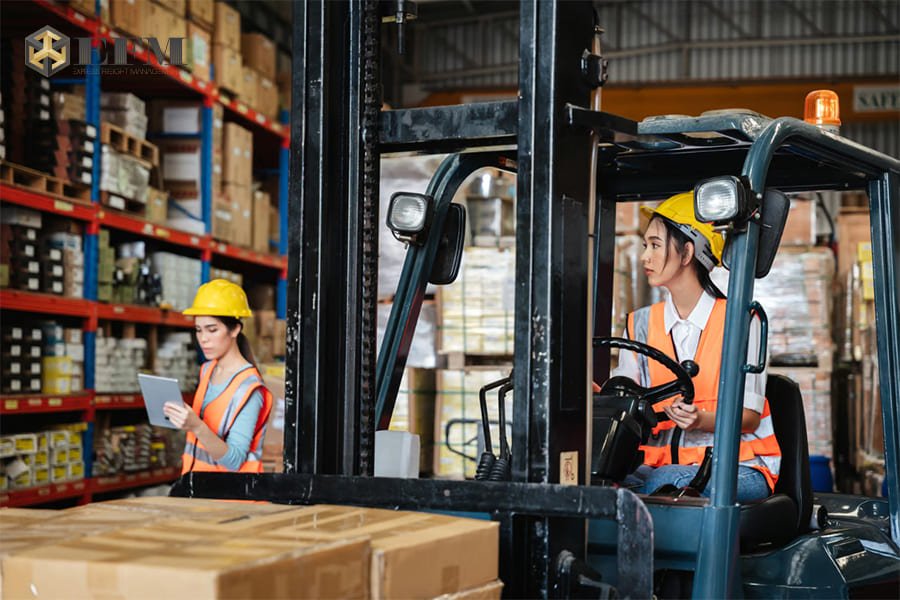
In today’s competitive logistics industry, efficient warehousing operations are key to a smooth supply chain. Lowering warehouse costs can boost profitability and improve service. The challenge lies in not sacrificing service quality, delivery speed, or inventory accuracy.
This article shares practical strategies to reduce warehousing costs, increase efficiency, cut waste, and enhance productivity.
1. Just In Time (JIT) Manufacturing: Reducing Storage and Waste
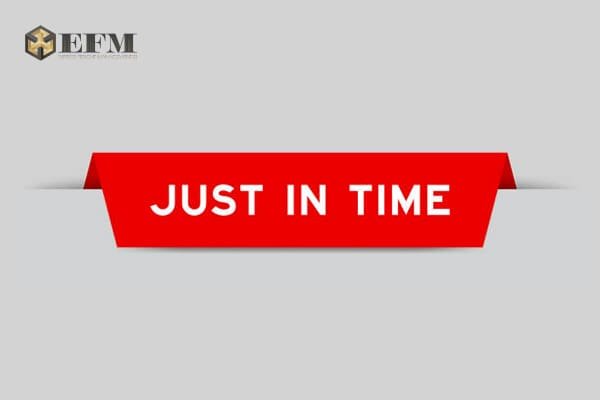
At the core of effective warehouse cost reduction is the Just In Time (JIT) manufacturing approach. JIT is designed to minimize inventory and streamline production by ensuring that materials are delivered only when needed. This reduces the need for large storage spaces, limits excess stock, and lowers inventory holding costs.
Benefits of JIT:
- Lower Holding Costs: By reducing the amount of stock in the warehouse, businesses can cut storage costs, insurance, and the risk of inventory becoming obsolete.
- Improved Cash Flow: With less capital tied up in unsold goods, companies can allocate resources elsewhere in the business.
- Waste Reduction: JIT systems reduce waste by ensuring that products are only produced or ordered in response to actual demand.
Implementation Tips:
- Work closely with suppliers to align delivery schedules with production needs.
- Leverage advanced demand forecasting tools to improve the accuracy of inventory needs.
- Implement automated ordering systems that trigger replenishment orders based on real-time data.
Real-world examples, like that of Honda, show that companies with successful JIT strategies often experience improved operational efficiency, reduced costs, and a quicker response to market changes.
2. Optimizing Warehouse Layout for Efficiency
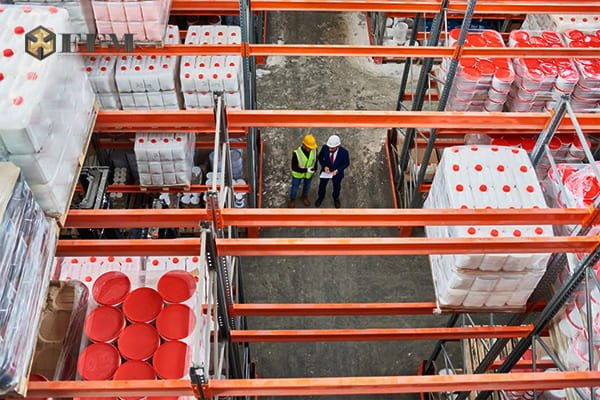
The layout of a warehouse is a critical factor in minimizing operational costs. An efficient warehouse design improves material flow, reduces handling times, and cuts labor costs. Poor layout can lead to unnecessary movement, time spent searching for items, and inefficiencies in inventory handling.
Techniques for an Optimized Warehouse Layout:
- Zoning: Organize the warehouse into specific zones based on product characteristics. For example, high-demand products should be placed in easily accessible areas. Conversely, slow-moving items can be stored farther from the picking areas.
- Cross-Docking: This method allows goods to be transferred directly from receiving to shipping, bypassing the storage process entirely. This reduces handling and storage costs, accelerating the order fulfillment cycle.
- FIFO (First In, First Out): Older inventory should be shipped first. This reduces the risk of stock obsolescence and spoilage. especially for perishable goods.
Investing in layout optimization reduces operational time and labor costs. It also boosts throughput, which directly improves shipping and customer satisfaction.
3. Streamlining Labor Management and Workforce Efficiency
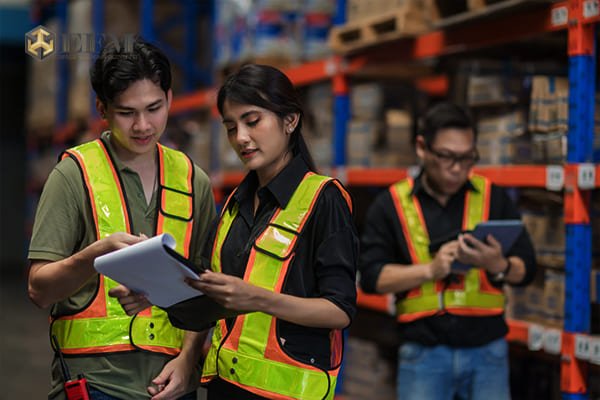
Labor accounts for a significant portion of warehouse operating costs. For companies dealing in international trade, these costs add up across multiple warehousing locations (e.g. Vietnam, Cambodia, etc.) The key to reducing these costs is maximizing workforce efficiency. This can be achieved through effective management and the strategic use of technology.
Labor Optimization Strategies:
- Task Specialization: Specializing tasks based on employee skills ensures that workers can perform tasks more efficiently. For example, employees dedicated to picking and packing will perform faster and with greater accuracy than those handling a variety of tasks.
- Cross-Training: Training employees to perform multiple roles creates a flexible workforce. This reduces downtime during shifts and helps accommodate for high turnover or absenteeism.
- Performance Monitoring: Implementing Key Performance Indicators (KPIs) helps monitor worker productivity. Tracking metrics like pick rates, accuracy, and time to complete tasks. This allows management to identify areas for improvement.
- Incentives and Rewards: Providing bonuses or other incentives for meeting performance targets. This can motivate employees to work more efficiently.
Businesses should ensure workers are well-trained, cross-functional, and appropriately incentivized. This helps improve output while reducing the need for overtime or temporary labor.
4. Reducing Inventory Holding Costs
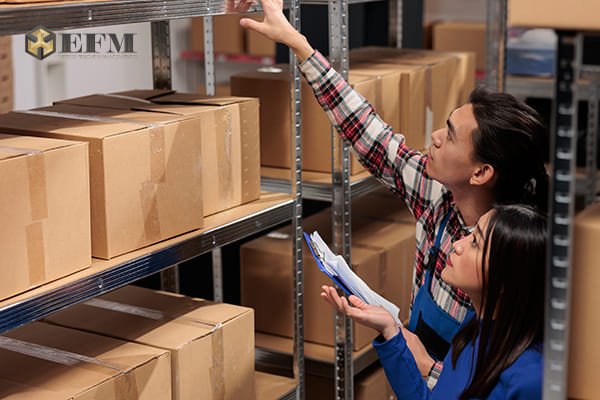
Inventory holding costs are a significant expense in warehousing. These costs include storage, insurance, depreciation, and the risk of obsolescence. By managing inventory effectively and improving turnover, businesses can dramatically reduce these costs. This, in turn, frees up capital and boosts operational efficiency.
Strategies to Lower Holding Costs:
- Improved Forecasting: Accurate demand forecasting helps ensure that stock levels match actual market demand. Using historical data, businesses can predict trends and avoid overstocking or stockouts.
- Inventory Turnover: Increase turnover rates by focusing on fast-moving products. The faster goods move in and out of the warehouse, the less storage space is required.
- Just-In-Case Stock vs. Just-In-Time: Consider carrying only a minimal buffer of safety stock, particularly for high-demand items. This approach helps balance risk and cost. It ensures you have enough stock to meet demand, while avoiding the overburdening of the warehouse.
- Seasonal Adjustments: Adjust inventory based on expected seasonal demand patterns. This prevents warehouses from storing excessive stock during off-peak periods.
Businesses can reduce holding costs through applying these strategies. More importantly, it ensures that the right products are always available for customers.
5. Automation and Technology Integration
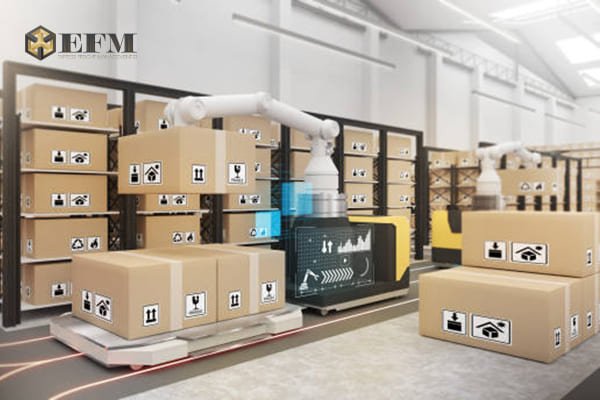
Here, automation refers to systems like automated picking and real-time inventory management. These technologies help cut labor costs and streamline operations, improving accuracy and speed. This is especially useful for businesses operating their own warehousing facilities.
Technologies to Consider:
- Automated Picking and Sorting Systems: Using robotics and conveyors to automate the picking, packing, and sorting of goods. These systems reduce reliance on manual labor and improve speed and accuracy.
- Drones for Stock Auditing: These drones would be equipped with RFID or barcode scanners. These help warehouses quickly perform inventory counts and audits. It reduces the time and cost of manual stock checks, particularly useful in large warehouses.
- Warehouse Management Systems (WMS): A WMS automates inventory tracking, order processing, and warehouse organization. Companies can track real-time inventory levels by integrating it with ERP systems. This manages orders more efficiently, and reduce stock discrepancies.
The cost of automation may be high upfront. However, the long-term savings on labor and operational efficiencies make it a worthwhile investment for many warehouses.
6. Transportation and Shipping Optimization
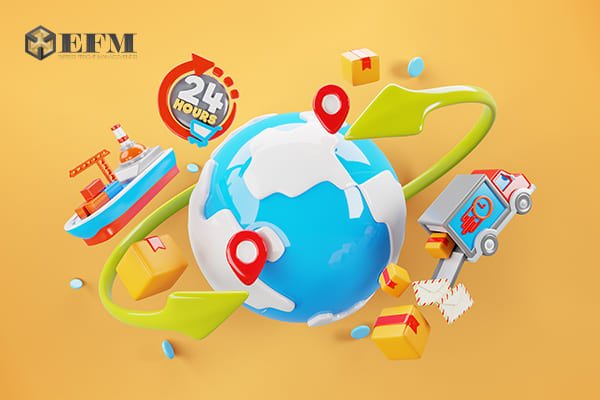
Warehouse operations do not exist in isolation—they are closely linked with transportation and shipping. This includes the different shipping options, like air freight, sea freight, trucking, and more. Optimizing these aspects can lead to significant cost reductions. This applies to both warehousing and logistics.
Further Reading: Choosing the Best Way to Ship: Air Freight vs. Sea Freight
Further Reading: Comparing Door-to-Door Sea Freight with Air Freight: Which is Right for You?
Shipping Optimization Strategies:
- Load Optimization: Maximize the use of available space in trucks to reduce the number of trips. This helps lower transportation costs and reduces the overall environmental impact.
- Route Planning: Advanced route planning software can help drivers choose the most efficient routes. This saves on fuel costs and reduces delivery times.
- Shipment Consolidation: Combining orders destined for the same location can reduce the number of shipments required. This lowers overall transportation expenses.
- Third-Party Logistics (3PL): Working with 3PL providers allow businesses to tap on their existing networks and economies of scale.
Optimizing transportation and shipping processes creates a more efficient supply chain. This enables warehouses to better manage costs across the entire logistics operation.
7. Outsourcing vs. In-House Operations
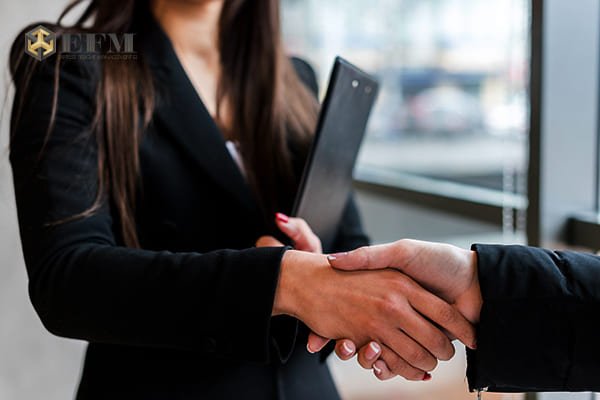
Businesses typically face two options when it comes to warehouse management. Outsource operations to a 3PL provider or keep them in-house. Each comes with its own set of pros and cons, which businesses have to balance to meet their specific needs.
Outsourcing Warehousing (3PL):
Pros:
- Cost Savings: 3PL providers have the infrastructure, technology, and workforce in place to handle warehousing efficiently. This is often at a lower cost than businesses could manage on their own.
- Scalability: Outsourcing provides flexibility in scaling operations. Businesses can adjust operations up or down without making a significant capital investment.
Cons:
- Less Control: Outsourcing means less direct control over warehouse processes and inventory management.
- Potential Coordination Issues: Communication gaps and misalignment between in-house and 3PL teams can lead to inefficiencies.
Further Reading: 3PL Meaning: Understanding the Role of Third-Party Logistics
In-House Warehousing:
Pros:
- Complete Control: Keeping warehousing operations in-house allows businesses to maintain full control. This includes control over their inventory, processes, and customer service.
- Customization: In-house teams can tailor operations specifically to the company’s needs.
Cons:
- Higher Initial Investment: Setting up and maintaining in-house operations can be expensive. The costs are particularly high for technology and infrastructure.
- Limited Scalability: Scaling in-house operations may require additional investments in space, equipment, and labor.
Choosing between outsourcing and in-house warehousing depends on several factors. These include business size, operational complexity, and available capital. Both approaches can result in cost savings if managed effectively.
Conclusion
Reducing warehouse costs is a multi-faceted effort. It requires careful consideration of various strategies. These include optimizing the warehouse layout, automating processes, and managing inventory more effectively. Implementing the right combination of techniques will improve your bottom line. It will also enhance overall supply chain efficiency and customer satisfaction.
By adopting a holistic approach to cost reduction, freight forwarders can create leaner, more agile warehouse operations. This can deliver significant savings without sacrificing service quality. Start by assessing your current operations, implementing small changes, and tracking their impact. The journey towards more efficient warehouse operations is continuous. However, the rewards are substantial for those willing to invest in smarter, more efficient practices.
Streamline your logistics with Express Freight Management – your trusted partner for seamless global shipping solutions. As a leading international freight forwarder based in the United States, we have successfully managed trades between the United States and Brunei, Cambodia, Indonesia, Laos, Malaysia, Myanmar, Philippines, Singapore, Thailand, and Vietnam for nearly two decades. With expert knowledge, advanced technology, and a commitment to reliability, we provide seamless logistics management that helps you focus on what matters most—growing your business.